Messehighlight 11. Oktober 2022
Beschichtungsanlagen für hochpräzise Optiken
1 / 3

EOSS 600
2 / 3

EOSS 500
3 / 3
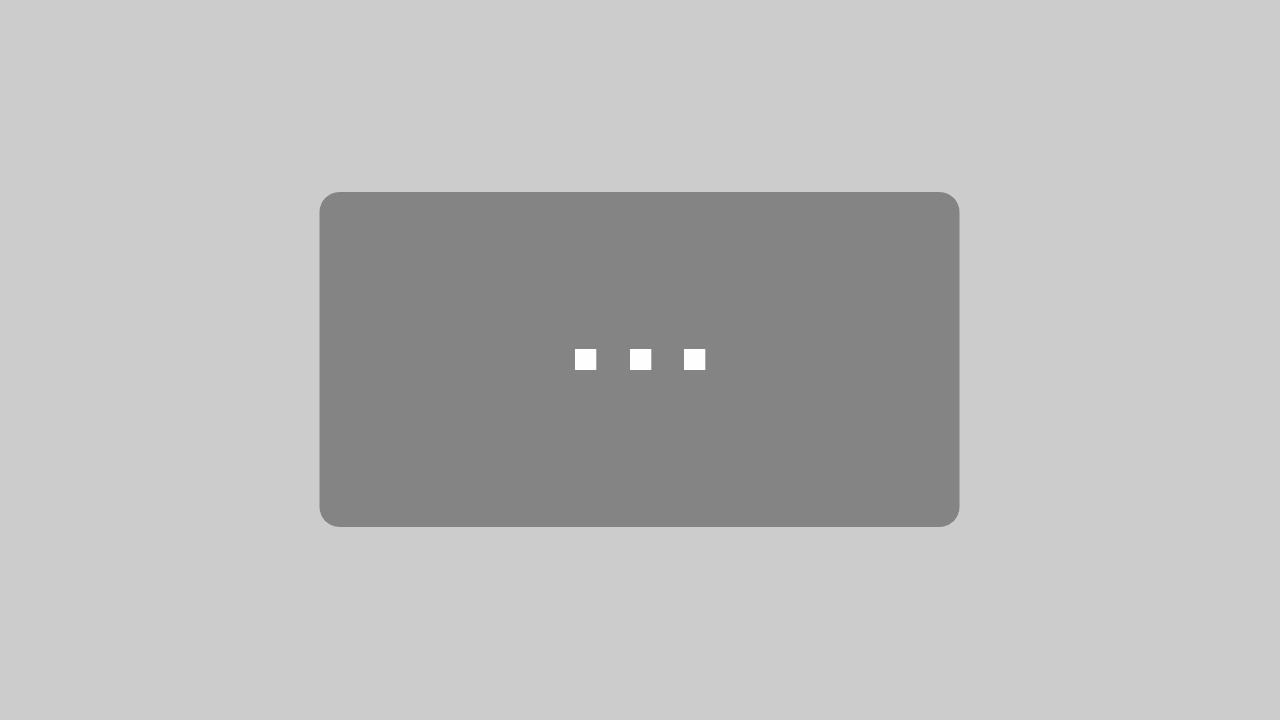
Mit dem Laden des Videos akzeptieren Sie die Datenschutzerklärung von YouTube.
Mehr erfahren
Interferenzbeschichtungen für optische Anwendungen erfordern eine hohe Gleichmäßigkeit der optischen Schichten und eine geringe Kontamination mit Defekten und Partikeln, um den Industriestandards für eine hohe Produktivität gerecht zu werden: eine gute Ausbeute und hohe Wiederholbarkeit der Abscheidung sind hier unser Ziel.
Die Produktserie FHR.Star-EOSS® bietet ein flexibles System, die alle Anforderungen auf Anhieb erfüllen kann: Das Konzept rotierender Doppelmagnetrons in Kombination mit einer Plasmaquelle in Sputter-up-Geometrie ermöglicht eine hohe Lebensdauer der Abscheidung, einen hohen Durchsatz und exzellente Schichtqualität mit geringer Absorption.
Unser Design ermöglicht den Anschluss von bis zu 4 verschiedenen Prozessgasen an jeder Sputterkammer und der Plasmaquelle, was eine große Anzahl möglicher reaktiver oder nicht reaktiver Sputterprozesse und die Abscheidung verschiedener Materialien mit unterschiedlichen physikalischen Eigenschaften ermöglicht. Diese Flexibilität erleichtert unseren Kunden den Produktwechsel mit minimalem Aufwand. Die Sputterkammern können mühelos getrennt werden, was einen schnellen Target-Material-Wechsel ermöglicht. Mit dem Öffnen des Deckels der Prozesskammer, ist ein einfacher Zugang zur Prozesskammer für Wartungstätigkeiten gewährleistet.
Vorteile von EOSS:
- Hervorragende Gleichmäßigkeit der Schichtdicke
- Qualität mit fehlerfreien Filmen
- Lange Targetlebensdauer durch Rotationstargets
- Vollautomatische Prozesssteuerung inklusive Stapelverarbeitung
- Rezeptprogrammgenerator für maximale Prozessflexibilität
- Einfache Wartung durch abnehmbare Prozesskammern und kippbaren Deckel der Prozesskammer
- Hervorragende Wiederholgenauigkeit und hohe Prozessstabilität
- Breitbandüberwachung für hochgenaue Schichtdickenkontrolle
- SEMI-Standard-Produktion auf Wafer-Level-Processing
Die Produktserie FHR.Star-EOSS® bietet ein flexibles System, die alle Anforderungen auf Anhieb erfüllen kann: Das Konzept rotierender Doppelmagnetrons in Kombination mit einer Plasmaquelle in Sputter-up-Geometrie ermöglicht eine hohe Lebensdauer der Abscheidung, einen hohen Durchsatz und exzellente Schichtqualität mit geringer Absorption.
Unser Design ermöglicht den Anschluss von bis zu 4 verschiedenen Prozessgasen an jeder Sputterkammer und der Plasmaquelle, was eine große Anzahl möglicher reaktiver oder nicht reaktiver Sputterprozesse und die Abscheidung verschiedener Materialien mit unterschiedlichen physikalischen Eigenschaften ermöglicht. Diese Flexibilität erleichtert unseren Kunden den Produktwechsel mit minimalem Aufwand. Die Sputterkammern können mühelos getrennt werden, was einen schnellen Target-Material-Wechsel ermöglicht. Mit dem Öffnen des Deckels der Prozesskammer, ist ein einfacher Zugang zur Prozesskammer für Wartungstätigkeiten gewährleistet.
Vorteile von EOSS:
- Hervorragende Gleichmäßigkeit der Schichtdicke
- Qualität mit fehlerfreien Filmen
- Lange Targetlebensdauer durch Rotationstargets
- Vollautomatische Prozesssteuerung inklusive Stapelverarbeitung
- Rezeptprogrammgenerator für maximale Prozessflexibilität
- Einfache Wartung durch abnehmbare Prozesskammern und kippbaren Deckel der Prozesskammer
- Hervorragende Wiederholgenauigkeit und hohe Prozessstabilität
- Breitbandüberwachung für hochgenaue Schichtdickenkontrolle
- SEMI-Standard-Produktion auf Wafer-Level-Processing